Magnesium Oxide Board vs. Traditional Materials: LEED Certification Impact Study
- JP Group MagMatrix Brand
- 4 days ago
- 17 min read
Magnesium oxide board brings a game-changing approach to eco-friendly construction right when we need it most. The construction industry now generates 37% of global carbon emissions, making it the biggest contributor to climate change. The sector's revenue will likely reach $14 trillion by 2027, which makes the search for greener building materials more important than ever.
Magnesium oxide material stands out with some impressive advantages over traditional options. These boards can resist fire and handle temperatures up to 1200°C, while standard drywall can't, so they provide better safety in fire-prone areas. The material's moisture absorption rate is just 0.34% compared to regular gypsum boards at 3%, which significantly cuts down mold risk. This magnesium oxide building material can be fully recycled and biodegraded. It helps projects earn vital LEED credits and reduces waste in an industry that's expected to create 2.2 billion tons of waste by 2025.
This piece will get into how MgO boards help with LEED certification in several ways. We'll look at everything from raw material use to energy performance and better indoor air quality.

Use of Sustainable Raw Materials for LEED MR Credit 6
Closed-loop manufacturing of magnesium oxide material
Magnesium oxide boards show how circular economy works through efficient closed-loop manufacturing systems. Companies recycle all process byproducts, including water, dust, and scraps during production. This creates a continuous material loop that cuts down waste and saves valuable resources.
Most facilities that make magnesium oxide boards use special systems to regrind and recycle manufacturing scraps back into production. On top of that, they capture, filter, and reuse water in later production batches. This detailed recycling system means facilities that follow best practices produce almost no waste.
The manufacturing process of magnesium oxide mgo board follows these precise steps:
Mixing natural components (we mainly used magnesium oxide and fillers) to form a thick paste
Molding the mixture into board shapes
Applying accurate first time and second time air-hardening curing technology to compact and strengthen the material to be with the sheets for the application of the fire rated structurally exterior sheathing, subfloor sheathing and roofing sheathing plus the sanded interior wall board and sanded backer board for interior lamination wallboard.
Cutting and finishing to get the final product
Some panels need to be extra-sanding process to make the sanded process plus to open the tongue & groove edges or tamper edges.
Many manufacturers have created patented low-energy techniques that work at room temperature technology curing room. This is a big deal as it means that unlike cement-based products that need extreme heat, this accurated controlled room-temperature processing cuts energy use by about 60%.
Looking at carbon emissions reveals more benefits. Magnesium oxide building material has a carbon footprint of about 37.3 kg CO2 eq/m²—22% less than Portland cement concrete alternatives. More than that, boards made with natural gas instead of coal cut CO2 emissions by another 18%.
The curing process absorbs carbon dioxide at the molecular level, which means some magnesium oxide panels might actually remove carbon from the atmosphere rather than add to it. This puts MgO boards in a special group of building materials that could help clean our air during their lifetime.
Reduced resource extraction compared to gypsum and cement
Traditional construction materials like gypsum and cement need large mining operations that harm landscapes and ecosystems. Magnesium oxide material comes from nowhere near as invasive methods.
Companies get magnesium oxide in two main ways: from natural magnesite deposits or from seawater and brine. Surface mining of magnesite needs no chemicals and barely disturbs the environment—even the small amount of dust created helps nearby land and ecosystems.
Here's how magnesium oxide board and gypsum board compare on environmental impact:
Magnesium oxide panels show even more environmental benefits in their makeup. These boards have:
No volatile organic compounds (VOCs)
No heavy metal salts
No crystalline silica
No hexavalent chromium
No asbestos
No toxic antifungal additives
This clean makeup makes them safer for construction workers and building occupants than traditional materials with potentially harmful chemical additives.
Gypsum doesn't last as long and creates more landfill waste when replaced. Magnesium oxide building material lasts longer. This means fewer replacements and less material needed over a building's lifetime.
Making magnesium oxide panels needs much less water than gypsum board production. Water efficiency matters more as construction grows in areas with water shortages.
The final product shows amazing differences in resource efficiency too. MgO boards are stronger and hold fasteners better than traditional cement-based materials. They resist fire as well as gypsum while handling impacts and water better. Unlike wood-based panels, magnesium oxide material stays the same size when wet, and unlike gypsum, it handles freezing and thawing without damage.
These combined benefits help projects earn LEED MR Credit 6 certification while performing better and having less environmental impact than traditional building materials.
Reduced resource extraction compared to gypsum and cement
Traditional construction materials like gypsum and cement need large mining operations that harm landscapes and ecosystems. Magnesium oxide material comes from nowhere near as invasive methods.
Companies get magnesium oxide in two main ways: from natural magnesite deposits or from seawater and brine. Surface mining of magnesite needs no chemicals and barely disturbs the environment—even the small amount of dust created helps nearby land and ecosystems.
Here's how magnesium oxide board and gypsum board compare on environmental impact:
Environmental Factor | MgO Boards | Gypsum Boards |
Raw Materials | Eco-friendly, fewer additives | Often includes synthetic additives |
Energy Use | More energy-efficient | Energy-intensive production |
Carbon Emissions | Lower CO₂ output | Higher CO₂ output |
Water Usage | Minimal consumption | Significant water requirements |
Recyclability | Highly recyclable | Limited recyclability |
End-of-Life Impact | Minimal landfill waste | Greater landfill contribution |
Toxicity | Non-toxic composition | Toxic gas is released when the fire burns |
Magnesium oxide panels show even more environmental benefits in their makeup. These boards have:
No volatile organic compounds (VOCs)
No heavy metal salts
No crystalline silica
No hexavalent chromium
No asbestos
No toxic antifungal additives
This clean makeup makes them safer for construction workers and building occupants than traditional materials with potentially harmful chemical additives.
Gypsum doesn't last as long and creates more landfill waste when replaced. Magnesium oxide building material lasts longer. This means fewer replacements and less material needed over a building's lifetime.
Making magnesium oxide panels needs much less water than gypsum board production. Water efficiency matters more as construction grows in areas with water shortages.
The final product shows amazing differences in resource efficiency too. MgO boards are stronger and hold fasteners better than traditional cement-based materials. They resist fire as well as gypsum while handling impacts and water better. Unlike wood-based panels, magnesium oxide material stays the same size when wet, and unlike gypsum, it handles freezing and thawing without damage.
These combined benefits help projects earn LEED MR Credit 6 certification while performing better and having less environmental impact than traditional building materials.
Packaging and Transport Efficiency for LEED MR Credits 2 and 4
Packaging and transportation systems are crucial to reducing the environmental footprint of construction materials. LEED Materials and Resources (MR) Credits 2 and 4 reward construction projects that cut down waste and use eco-friendly materials. MgO board manufacturers have created smart packaging approaches that help achieve these certification goals.
Palletization and reduced packaging waste
MgO panel transportation uses advanced palletization techniques that cut down packaging material needs. This organized packaging approach offers several key benefits:
The palletization creates compact shipping arrangements that fit more MgO boards in each shipment. Manufacturers can load more products into delivery vehicles by arranging panels on standard pallets. This cuts down the number of trips needed and leads to lower carbon emissions from transportation.
The pallet system protects products well while using minimal materials. Unlike other construction materials that need individual wrapping or extra protection, MgO building materials need less protective packaging. MgO boards' natural durability helps here - they resist moisture, impact, and warping, so they don't need as much protection during shipping.
The palletized shipping method for MgO material improves logistics in several ways:
Standard dimensions help optimize warehouse storage
Machine handling needs less labor and prevents damage
Same-sized pallets help load trucks efficiently
Quick loading and unloading means less vehicle idling
These benefits support LEED MR Credit 2's focus on construction waste management. Projects need to keep construction debris out of landfills and incinerators. MgO panels' minimal packaging helps projects reach the 50-75% waste reduction targets for this credit.
Use of recycled and reusable packaging materials
MgO board manufacturers also prioritize eco-friendly packaging materials. Their commitment shows through several practices:
The protective covers for MgO panels often contain recycled plastics and papers. These materials get a new life protecting construction materials instead of ending up in landfills. The recycled content usually meets LEED MR Credit 4 requirements.
Reusable packaging gives MgO board distribution another green advantage. Manufacturers use sturdy straps and corner guards that last for multiple trips rather than single use. These parts go back to factories for inspection and reuse, creating a closed loop that matches circular economy goals.
Wooden pallets for MgO panel shipments often join pallet exchange programs, moving between manufacturers, distributors, and construction sites. Good pallets stay in use instead of becoming waste. When pallets wear out, manufacturers make sure they go to wood recycling instead of dumps or incinerators.
The smart packaging approach for MgO building material helps with LEED certification:
LEED Credit | Packaging Contribution |
MR Credit 2 | Reduced packaging waste volume |
MR Credit 2 | Higher percentage of recyclable packaging materials |
MR Credit 4 | Incorporation of recycled content in packaging |
MR Credit 4 | Use of regionally available packaging materials |
These packaging practices show how MgO panel manufacturers have improved both their product and delivery system to support green construction goals. Their focus on reducing packaging and choosing better materials creates an approach that matches LEED certification needs while cutting environmental impact across the supply chain.
Construction Waste Reduction for LEED MR Credits 2.1 and 2.2
Projects need to divert 50% and 75% of waste from landfills to achieve LEED MR Credits 2.1 and 2.2. Magnesium oxide building material has many advantages that help meet these standards. Its installation features and complete recyclability make it an excellent choice.
On-site installation with minimal cutting waste
Magnesium oxide panels create less on-site waste than traditional building materials. These boards let you attach most cladding types directly without extra metal or aluminum parts. You won't need the usual girts, sub-girts, rails, or clips for cladding attachment.
MgO board installations produce minimal waste for several reasons:
Precision Manufacturing: MgO boards come with exact dimensions that reduce the need for extra cutting and trimming at construction sites.
Structural Integrity: These boards are extremely durable. They rarely get damaged during transport and handling, which means less waste at jobsites.
Versatile Installation Methods: You can score, snap, saw, drill, and fasten these panels to wood or steel framing. This flexibility helps reduce cutting waste.
Advanced Edge Systems: Some MgO board products feature 4-sided shiplap joints. These create exact connections without visible fasteners and minimize material loss during installation.
These panels work as Structural Insulated Sheathing by combining MgO board with other layers. They replace multiple traditional materials, which reduces overall waste at construction sites. This feature helps achieve LEED MR Credits 2.1 and 2.2, which focus on waste diversion and eco-friendly disposal.
Leftover material rarely goes to waste. You can use extra pieces of magnesium oxide building material to edge gardens, build shelves, or create surfaces for hot pots and plates. Even small pieces remain useful instead of becoming waste.
Recyclability of magnesium oxide panels
Magnesium oxide panels' recyclability helps reduce construction waste. Without doubt, this makes them perfect for projects seeking LEED MR Credits 2.1 and 2.2 certification.
MgO boards can be recycled in several ways:
Reusing Broken Pieces: You can repurpose larger broken pieces where smaller panels are needed.
Grinding and Repurposing: Ground MgO material works as filler in new construction materials, including new MgO boards. It also works well in cement-based applications or as a soil additive.
Biodegradability: MgO board qualifies as "nutritional waste". Ground-up boards can enrich soil with nutrients. They break down into MgO, Mg(OH)2, MgSO4, which provide magnesium for plant growth and soil balance.
Traditional building materials don't match up. Portland cement waste has few recycling options and usually ends up in landfills. Gypsum faces strict disposal rules, especially in the UK. It can't go into landfills with biodegradable materials because it releases hydrogen sulfide.
Magnesium oxide panels reduce waste throughout their life. They last longer than drywall or plywood and need fewer repairs. They resist water damage and mold. This means less replacement waste over time.
MgO board manufacturers design their products to match LEED waste management principles:
Production creates minimal waste
Leftover material is easy to recycle or reuse
Boards are completely recyclable and biodegradable
They count as clean and nutritional waste
These features help projects reach waste diversion goals for LEED MR Credits 2.1 and 2.2. Using magnesium oxide panels reduces environmental impact while helping achieve LEED certification.
Reusability and Disassembly for LEED MR Credits 3.1 and 3.2
Reusability is the life-blood of environmentally responsible building practices. Magnesium oxide board has proven to be an exceptional material for projects seeking LEED MR Credits 3.1 and 3.2. These credits reward construction projects that use salvaged, refurbished, or reused materials. This approach reduces the need for virgin resources and minimizes construction waste.
Screw-fastened MgO board removal and reuse
MgO panels work great for building disassembly when builders use the right fastening techniques. These boards can be repurposed effectively if attached with screw fastening methods. This allows removal without damage and future reuse. The boards help achieve LEED MR Credits 3.1 and 3.2, as these credits reward projects that use reusable building components.
The installation process for magnesium oxide material includes:
Using corrosion-resistant fasteners for secure attachment
Using screws with self-counter boring heads for easy installation
Using gun nails for wood and light gage steel framing applications
The panels keep their structural integrity during removal, which makes them valuable. Traditional drywall crumbles and becomes waste during renovations. MgO board, however, can be unscrewed carefully and saved for future use. This creates a circular materials economy in building projects.
This reuse factor matters more as renovation projects seeking LEED certification must show specific percentages of reused materials. One project example showed that reusing materials worth 46.41% of total materials cost earned one LEED point. Projects reaching 60% qualified for exemplary performance recognition.
Durability enabling multiple lifecycle uses
MgO building material's natural durability allows remarkable reuse across multiple building lifecycles. These boards maintain their performance through numerous applications, unlike conventional materials that degrade after one use.
The material's exceptional physical properties create this durability. MgO board has excellent impact strength that extends structure's lifespan. The panels resist moisture, humidity, fire, insects, fungus, mold, mildew, and chemicals. This ensures they stay functional even after years in demanding environments.
MgO boards' structural stability offers another key advantage. The panels stay intact when slightly bent and won't warp, swell, or delaminate after brief moisture exposure. This makes them perfect candidates for salvage during building renovations or demolitions.
MgO panels can be reused in several ways:
Direct reuse in new construction without modification
Cutting into smaller pieces for alternative applications
Repurposing in non-structural applications like decorative elements
Building owners and contractors get real benefits beyond LEED certification. Salvaged materials cost less than new ones, which cuts construction expenses while earning LEED credits. Projects move faster because teams don't wait for new material delivery.
MgO board's end-of-life flexibility boosts its sustainability profile. Teams can grind these panels into inorganic filler material or soil nutrients when reuse isn't possible. This beats Portland cement waste that fills landfills and gypsum disposal that faces stricter rules due to hydrogen sulfide release concerns.
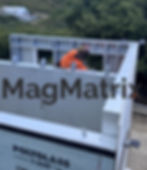
Indoor Air Quality Compliance for LEED EQ Credits 4.1 to 4.4
The quality of indoor air starts with choosing the right materials. LEED acknowledges this through its Environmental Quality credits. LEED EQ Credits 4.1 to 4.4 aim to reduce indoor air contaminants that could harm people's health and comfort. Magnesium oxide board stands out as an excellent material choice to earn these credits because of its clean emission profile and non-toxic makeup.
Zero VOC emissions from magnesium oxide mgo board
Volatile Organic Compounds (VOCs) pose serious health risks in indoor spaces. Construction materials usually release these compounds slowly and reduce air quality throughout a building's life. But magnesium oxide panels are different from regular options because they contain almost no VOCs. This makes them excellent for better indoor air quality.
Magnesium oxide building material holds a special place in the LEED certification system. MgO boards belong to the "Inherently Non-Emitting" category for LEED purposes. This means these materials naturally don't release VOCs, so they meet full compliance without needing extra VOC emissions tests.
The LEED EQ Credit system needs specific testing protocols for different building materials:
EQ Credit 4.1: Focuses on adhesives and sealants
EQ Credit 4.2: Addresses paints and coatings
EQ Credit 4.3: Concerns flooring systems
EQ Credit 4.4: Reviews composite wood and agrifiber products
Each category must meet strict emissions criteria based on the California Department of Health Services Standard Practice for Testing Volatile Organic Emissions. Magnesium oxide mgo board naturally meets these requirements because it only contains natural minerals and reinforcing fibers without chemical additives that could off-gas.
No formaldehyde, asbestos, or phenolics
Magnesium oxide material's clean composition creates a clear difference from traditional building materials. Many standard options contain chemicals that cause health issues:
Material Type | Potential Harmful Contents |
Plywood | Formaldehyde, adhesives |
Drywall | Chemical additives, potential mold growth |
Particleboard | Urea-formaldehyde resins |
MgO Board | None - natural minerals only |
Regular materials like plywood and drywall often contain formaldehyde, asbestos, and ammonia. These substances leak into indoor air over time and can trigger allergies, asthma, and lead to more serious health issues. Many traditional composite wood products also contain urea-formaldehyde resins that LEED EQ Credit 4.4 specifically prohibits.
Magnesium oxide board achieves its health-friendly profile through its simple composition - magnesium oxide, magnesium chloride, and reinforcing fibers. This natural formula means no toxins escape into indoor environments. Manufacturers always point out that MgO panels contain:
No formaldehyde or toxic binders
No asbestos
No phenolics or resins
No crystalline silica
No carcinogens
This clean makeup helps earn LEED EQ Prerequisite 1, EQ Credit 1, and EQ Credits 4.1-4.4. The absence of harmful substances creates safer construction sites for workers and healthier spaces for building occupants.
Healthcare settings, schools, and homes benefit greatly from magnesium oxide panels. The zero-emissions profile creates spaces where sensitive people can thrive without exposure to airborne toxins. This becomes especially important in facilities that serve vulnerable populations like hospitals, where indoor air quality affects patient recovery.
These air quality benefits last throughout magnesium oxide building material's entire life cycle. The panels keep their emissions-free profile from installation through occupancy and even during renovations, which helps maintain healthy indoor environments consistently.
Energy Performance Contribution for LEED EA Prerequisite 2
Building energy efficiency is a key part of LEED certification, and material selection helps achieve compliance standards. LEED EA Prerequisite 2 sets minimum energy performance requirements that certified projects must meet. These requirements aim to reduce environmental effects from excessive energy use.
Thermal insulation properties of MgO panels
Magnesium oxide board shows remarkable thermal insulation characteristics that set it apart from regular construction materials. The thermal conductivity value of 0.038 W/mK means MgO panels are a big deal as they outperform traditional options like drywall (0.160 W/mK) and cement board (0.130 W/mK). Heat transfers more slowly through MgO panels because of this lower thermal conductivity, which creates more energy-efficient building envelopes.
Magnesium oxide material demonstrates these insulation benefits through several performance advantages:
Heat transfer minimizes through walls, ceilings, and floors
Thermal bridging reduces across structural elements
Temperature regulation improves in extreme climates
Heating and cooling systems need less energy
These thermal properties help keep indoor temperatures comfortable while reducing the building's overall energy use. MgO board maintains consistent thermal performance in different climate zones, making it ideal for ground applications in various regions.
Improved building envelope efficiency
MgO panels help meet LEED EA Prerequisite 2 requirements effectively. Ground applications show that MgO panels achieve a 10% performance boost for new constructions or a 5% improvement for renovated existing buildings, as outlined by the ANSI/ASHRAE/IESNA Standard 90.1.
MgO building material provides even better efficiency benefits when used in structural insulated sheathing (SIS) systems. The thermal control layer becomes continuous and works better than similar systems – even those using thermally-isolated attachment methods. This integration allows simpler wall designs that keep optimal thermal performance while reducing complexity.
Several factors affect efficiency:
Factor | Impact on Efficiency |
Panel thickness | Thicker panels provide higher R-values |
Installation method | Continuous coverage maximizes performance |
Climate zone | Performance benefits increase in extreme climates |
Building design | Optimization with other systems improves results |
These performance characteristics help projects earn points in the Energy and Atmosphere category, which offers up to 33 points for commercial projects. Better thermal performance specifically addresses EA Prerequisite 2: Minimum Energy Performance goals, one of four required credits in this category.
MgO panels' building envelope improvements affect operational costs throughout a structure's lifetime. This creates long-term economic benefits and environmental advantages.
End-of-Life Management for LEED MR Credit 5
The environmental lifecycle of construction materials reaches way beyond their functional use period. LEED MR Credit 5 rewards projects that manage materials properly when their useful life ends. Magnesium oxide board shows exceptional credentials in this area.
Biodegradability and landfill-safe disposal
Magnesium oxide panels qualify as "clean and nutritional waste" after their service life ends. Traditional construction materials often release harmful gasses in landfills, but MgO boards pose minimal environmental threats whatever the disposal method.
The magnesium oxide building material's inert nature will give a safe burial option in landfills without contaminating land, streams, or water bodies. This non-toxic composition sets it apart from conventional options that need special disposal procedures.
The sort of thing I love about magnesium oxide mgo board is knowing how to break down naturally over time. The decomposition creates various magnesium compounds (MgO, Mg(OH)₂, MgSO₄) that nourish soil instead of polluting it.
Recyclability into road base or soil additive
Magnesium oxide material follows several recycling pathways that contribute meaningfully to LEED certification requirements:
Recycling Method | Environmental Benefit |
Soil amendment | Provides nutrients for plant growth |
Road base material | Reduces demand for virgin resources |
Filler in new construction | Creates circular material economy |
Wastewater treatment | Helps purify contaminated water |
The recycling process usually involves collecting MgO boards from construction or demolition sites. Workers remove impurities like paint, grind them into smaller pieces, and separate any contaminants. The refined particles can then serve multiple applications.
Magnesium oxide building material serves extensively in soil and groundwater remediation, wastewater treatment, drinking water purification, and air emissions treatment. These applications show how MgO board continues to deliver environmental benefits rather than imposing ecological costs, even at its lifecycle's end.
Regional Material Sourcing for LEED MR Credit 5.1
Local sourcing is key to green construction practices. LEED MR Credit 5.1 rewards construction projects that use building materials extracted, harvested, recovered, and manufactured within 500 miles of the project site. Magnesium oxide board lines up perfectly with these requirements because of its unique sourcing options.
Availability of magnesium oxide from seawater and brine
Natural sources around the world can provide magnesium oxide material. Seawater has an average Mg²⁺ concentration of 1.29–1.35 g/L, which makes it one of the most important sources of magnesium. Natural brines offer another great way to extract this material. This wide availability lets companies set up production facilities near coastlines or brine deposits.
The extraction process typically involves:
Precipitating magnesium hydroxide from seawater or brine
Processing the precipitate into magnesium oxide
Refining the material for construction applications
Desalination plants have become a crucial source for magnesium oxide production. The reject brine that comes from desalination contains concentrated magnesium that companies can recover through precipitation methods. This creates a valuable connection between water treatment and construction material production facilities.
Reduced transportation emissions for local projects
Using magnesium oxide panels from nearby sources cuts down transportation-related carbon emissions. This is a big deal as it means that projects using local magnesium oxide building material can meet LEED requirements, which ask for at least 10% of materials (based on cost) to come from within 500 miles of the site.
Shorter transportation distances mean a smaller carbon footprint. Manufacturing facilities near coastlines or brine sources also help reduce the environmental impact of moving raw materials.
China used to dominate global magnesia production. Production facilities have sprung up worldwide near seawater resources. This growing distribution network helps construction projects source magnesium oxide building material locally and earn valuable LEED MR Credit 5.1 points without compromising on quality or performance.
Conclusion
This complete analysis shows how magnesium oxide boards provide exceptional advantages to LEED certification in many categories. These innovative panels reshape the scene of eco-friendly construction with their remarkable environmental profile. MgO boards outperform traditional materials and generate 22% less carbon footprint than Portland cement alternatives. They also provide better fire resistance, moisture resistance, and structural integrity.
MgO material's unique features include a closed-loop manufacturing process, minimal waste, and total recyclability. Projects can earn LEED certification points from MgO panels' contributions to several credit categories. These range from eco-friendly raw materials and reduced construction waste to better indoor air quality and energy performance. These boards are a great way to get healthier indoor spaces because they don't contain VOCs, formaldehyde, asbestos, or other harmful substances.
Environmental advantages continue well past the construction phase. MgO building material stays eco-friendly throughout its lifecycle - from production to installation, use, and final disposal or recycling. The boards' biodegradability as "nutritional waste" makes them revolutionary compared to traditional materials that create disposal issues and harm the environment.
The construction industry needs an all-encompassing approach that goes beyond single-point solutions. MgO boards illustrate this complete philosophy by meeting multiple sustainability criteria at once. Their growing availability from seawater and brine sources makes them even more viable as truly sustainable building materials.
Construction professionals who want both LEED certification and superior performance should think about MgO panels as their material of choice for modern, environmentally responsible building projects.
Brand old website: www.magmatrixboards.com
Group new website: www.jinpenggroups.cn