7 Best Subfloor Options That Won't Break Your Bank in 2025 -- MagMatrix BMSC 517 New Sulfate MGO Subfloor Panels Advantages
- JP Group MagMatrix Brand
- 1 minute ago
- 15 min read
Your wallet doesn't need to suffer while looking for the best subfloor options. Research shows that moisture problems affect at least 60% of basements. This makes your choice of subfloor a vital part of protecting your home.
My years of hands-on experience with different materials have taught me something important. A basement subfloor does more than provide foundation support. It serves as a significant barrier between your finished floor and base floor that regulates moisture and temperature. Many homeowners don't know about budget-friendly alternatives to traditional plywood and OSB subfloor materials. DRIcore provides a solid option at $1.89 per square foot. A single layer of 7/16" OSB costs considerably less at $0.61 per square foot. Products like QuietBoard offer versatility - you can float, staple, or glue them under floor coverings such as vinyl planks and engineered wood.
This piece explores seven affordable subfloor solutions available in 2025. You'll learn about traditional methods and state-of-the-art options like MGO subfloor panels. These choices deliver excellent results for basement finishing, renovations, or new construction projects while keeping your budget intact.
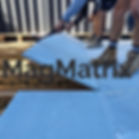
AdvanTech Subfloor Panels for Subfloor Options
AdvanTech subfloor panels stand out as a premium choice that builders across the country trust. These engineered panels have ranked #1 in quality every year since 2002 according to builder surveys. Let me show you why you might want these panels in your next flooring project.
AdvanTech Subfloor Panels key features
AdvanTech panels are different from regular OSB or plywood. They use advanced liquid resin technology that really coats each wood strand during manufacturing. This creates a reliable moisture barrier through the whole panel, not just the surface. The panels come with:
·      High-density wood composition that gives superior strength and stiffness
·      Advanced moisture-resistant resin technology throughout the panel
·      Great fastener-holding power that keeps floors flat and quiet
·      Precision tongue and groove profile with patented fastening guides that make installation easier
·      Structural 1 rating beyond standard building code requirements
The panels come in different thicknesses, with performance categories from 19/32" to 1-1/8". Each size works for specific span ratings from 20 oc to 48 oc. The manufacturing process creates the perfect strand thickness and dimension. This builds a woven matrix of fibers that balances stiffness and dimensional stability.
AdvanTech Subfloor Panels pros and cons
Pros:
·      Moisture resistance stops swelling, warping, cupping, and delamination
·      Design strength gives you a quality, stiff floor with minimal bounce
·      Strong fastener-holding power cuts down on nail pops and floor squeaks
·      Limited lifetime warranty and 500-day no-sanding guarantee back the product
·      No added urea formaldehyde makes it a low-emitting material
·      Structural-1 rating gives better resistance to wind and seismic loads
Cons:
·      Costs more upfront than standard OSB or plywood subfloors
·      Not rated for exterior use; classified as Exposure 1 under PS-2
·      You need proper spacing (1/8" gap) between panels during installation
·      Requires adhesive to work best, which adds to installation cost
AdvanTech Subfloor Panels pricing
These panels cost more than basic OSB or plywood. Current market prices look like this:
·      23/32" (3/4") 4'x8' panels: About $33.60 per sheet
·      1-1/8" panels: Higher price point but maximum stability
Many builders say the extra upfront cost pays off. One pro put it this way: "I spend a little more on this subfloor than I have in the past. The elimination of problems makes it totally worth it".
AdvanTech Subfloor Panels best use cases
These panels work best in:
1.    High-end residential construction - When floor quality and quiet operation matter most
2.    Moisture-prone environments - Perfect for basements and areas that might see moisture during construction
3.    Under premium flooring materials - Works great under:
·      Hardwood flooring - Dense wood holds fasteners tight
·      Ceramic tile and natural stone - Reduces risk of cracked tile
·      Carpet - Gives a flat, stable base
4.    Multifamily construction - When you need to cut down noise between units
Regular plywood or OSB can soak up moisture and cause issues later. AdvanTech's moisture resistance and structural strength make it perfect when quality matters most. Builders love that they get fewer callbacks about squeaky or uneven floors, which keeps customers happy.
DRIcore Subfloor Tiles
DRIcore makes a floating subfloor system that turns cold, damp concrete floors into warm, comfortable living spaces. DIY homeowners will find these 2'×2' panels easy to work with. The panels combine oriented strand board (OSB) with a high-density polyethylene moisture barrier base. They work great for basements and other concrete surfaces.
DRIcore Subfloor Tiles key features
DRIcore's patented Air Gap Technology sits at the heart of its design. The raised polyethylene pattern underneath creates constant airflow beneath the panels. This smart design lets moisture from concrete evaporate naturally instead of getting trapped. Each panel is 23.25"×23.25" and 3/4" thick, which adds minimal height to your floor.
These panels come with a tongue and groove edge that makes them super easy to put together. You won't need glue or special tools. The panels connect just like a floating floor system. You could finish a 500 sq. ft. room in one afternoon. The engineered wood core is really strong too - it can hold up to 6,642 pounds per square foot.
Want better insulation? The R+ model has an extra layer of extruded polystyrene foam. Regular DRIcore panels give you an R-value of 1.4. The R+ version steps this up to 2.7. You'll notice the difference when it comes to blocking cold from concrete.
DRIcore Subfloor Tiles pros and cons
Pros:
·      Blocks moisture and helps prevent mold, mildew, and minor water leaks
·      Raises floor temperature by about 6°F with thermal break technology
·      No need to anchor to concrete in most cases (true floating system)
·      Light panels (about 7 lbs each) make handling easy
·      Works with all flooring types - carpet, laminate, vinyl, engineered hardwood and ceramic tile
·      You can cut panels with basic tools like circular saws or jigsaws
Cons:
·      Costs much more than regular subfloor options
·      Standard version doesn't insulate well (only 1.4 R-value)
·      Tiled areas need extra fastening to concrete
·      Won't work where height is tight (adds 3/4" or 1" for R+ version)
DRIcore Subfloor Tiles pricing
Standard DRIcore panels run between $6.00-$9.00 per 2'×2' panel (4 square feet). The R+ version costs more at $10.00-$15.00 per panel. Home Depot usually sells the standard version for about $6.97 per panel.
A 1,200 square foot basement needs around 300 panels. That means you'll spend about $2,100-$2,700 for standard panels or $3,000-$4,500 for R+ panels. It's a big investment compared to regular subfloors, but many homeowners say the benefits make it worth the cost.
DRIcore Subfloor Tiles best use cases
DRIcore shines in these situations:
5.    Basements with moisture concerns: The airflow design helps reduce minor moisture problems without major waterproofing.
6.    DIY renovations: Homeowners love the easy-to-handle panels and simple installation process.
7.    Cold concrete floors: The thermal break makes basement floors feel much warmer.
8.    Underneath floating floors: These panels work great with laminate, vinyl plank, and engineered hardwood click-lock systems.
9.    Areas with minor floor irregularities: The panels can handle slight unevenness up to 1/4" without extra floor prep.
DRIcore works well in garages, workshops, and bathrooms too, but each needs special installation steps. Bathroom installations or areas near showers need flexible caulking to seal gaps between finished flooring and fixtures.
PVC and WPC Boards
Wood-plastic composite (WPC) and polyvinyl composite (PVC) boards are game-changing alternatives in the subfloor market. These boards blend natural and synthetic materials to create options that work great in places with moisture problems.
PVC and WPC Boards key features
WPC boards give you the best of both worlds. They contain 70% virgin polymer, 15% additive chemical, and 15% wood powder. This mix creates a material that looks like wood but lasts longer and handles moisture better. Manufacturers use high-temperature extrusion or injection molding to combine these components smoothly.
PVC boards mainly contain polyvinyl chloride with various additives. Both materials beat traditional wood-based products with:
·      Better moisture resistance that works great in basements and bathrooms
·      Protection against termites that regular wood doesn't have
·      UV ray resistance to prevent color fading outdoors
·      A closed-cell structure that keeps water out
·      The ability to work with different flooring systems
WPC's core comes with a printed vinyl layer and wear layer on top. This creates a complete flooring system you can install even on uneven subfloors. Thicker variants (20-25mm) make the best subfloors because they provide great support and last longer.
PVC and WPC Boards pros and cons
Pros:
·      These boards handle water amazingly well in damp areas
·      They feel more comfortable under your feet than cement options
·      Sound absorption helps cut down noise between floors
·      You won't need regular sealing or painting
·      Many options use recycled materials, making them eco-friendly
·      They resist rot, rust, and chemical damage for years
·      Extreme weather won't make them warp
Cons:
·      Temperature changes can make them expand and contract
·      They cost more upfront than regular subfloor materials
·      Regular PVC foam boards might not be tough enough for direct flooring
·      WPC might fade in sunlight more than natural wood
·      Some types can warp or buckle when they get too hot
·      The finish might not look as good as natural wood
PVC and WPC Boards pricing
WPC and PVC board prices change based on how thick they are, their quality, and what you're using them for. Here's what you'll find in the market:
Type | Thickness (mm) | Price Range (USD/m²) | Application |
WPC Outdoor Flooring | 20-30 | $12-30 | <citation index="63" link="https://www.hosungdeck.com/wpc-industry-trends/wpc-panel-prices/" similar_text="Application |
WPC Indoor Panels | 10-15 | $8-20 | <citation index="63" link="https://www.hosungdeck.com/wpc-industry-trends/wpc-panel-prices/" similar_text="Application |
PVC WPC Boards | 10-20 | $10-25 | <citation index="63" link="https://www.hosungdeck.com/wpc-industry-trends/wpc-panel-prices/" similar_text="Application |
PVC Foam Board | Varies | ₹95/sq ft ($1.15/sq ft) | Commercial applications |
WPC flooring costs more than standard LVT products but less than natural wood flooring. You'll usually pay between $2.00 and $7.00 per square foot.
PVC and WPC Boards best use cases
WPC and PVC boards work best in these situations:
10. Moisture-prone environments - They're perfect for basements, bathrooms, and kitchens because they're waterproof
11. Areas requiring thermal insulation - Their composite structure insulates better than concrete or standard OSB
12. Spaces with minor flooding concerns - You can recover more easily after water issues because they resist water
13. Areas with termite problems - These boards won't attract insects like regular wood does
14. Renovation projects with uneven subfloors - WPC can handle small imperfections without much prep work
Commercial spaces with heavy foot traffic benefit from the tough wear layer. These materials also work great as subfloors in multi-story buildings because they reduce noise between floors.

Double Layer Plywood Subfloor
Builders have trusted double layer plywood subfloor systems as reliable foundations for high-performance flooring for decades. This time-tested method combines strength and stability. The strategic layering approach distributes weight and keeps movement minimal.
Double Layer Plywood Subfloor key features
A double layer plywood system has two separate layers of wood panels in a specific setup. The original layer uses 3/4" CD Exposure 1 Plywood (CDX) or 3/4" OSB panels attached right to floor joists. The second layer typically has 1/2" CD Exposure 1 Plywood panels on top of the base layer.
The right installation technique makes a big difference:
·      Second layer panels should be offset by 1/2 panel in each direction from the base layer
·      You can also install the second layer diagonally or perpendicular to the first layer
·      Panels need 1/8" spacing between sheets to expand
·      Fastening should follow a 12" minimum grid pattern with ring-shanked nails or staples
The right panel spacing plays a vital role. You should keep 1/16" to 1/8" gaps around panel edges and 3/4" gaps at vertical obstructions. This prevents buckling as seasons change. Both layers must meet U.S. Product Standard PS 1 or PS 2, or Canadian standards CSA O121, O151, O325, or 0437.
Double Layer Plywood Subfloor pros and cons
Pros:
·      Stronger and more stable than single-layer systems
·      Staggered seam design cuts down deflection and squeaks
·      Better distribution of loads across the floor system
·      Less seasonal movement that causes floor problems
·      Provides a stiffer base for brittle flooring materials like tile
·      You won't need extensive Tapcon fastening over concrete slabs
Cons:
·      Materials cost more than single-layer options
·      Takes longer to install and is more complex
·      Floor height increases more than single-layer systems (about 1/2")
·      You must watch fastener length to avoid going through both layers
·      Extra weight might matter in some cases
Double Layer Plywood Subfloor pricing
Today's market shows a wide range in double layer plywood subfloor installation costs:
Component | Cost Range (July 2025) |
Base installation | $4.11-$6.28 per square foot |
Additional layer | Approximately $10,000 for whole-home coverage |
Regional labor costs, material availability, and project specs affect pricing. This system needs substantial investment. In spite of that, builders say it's worth it for better floor performance.
Double Layer Plywood Subfloor best use cases
These systems work best in specific situations:
15. Beneath brittle flooring materials - You must have this rigid foundation under tile or natural stone, especially with wide joist spacing
16. High-traffic commercial settings - The extra strength and load distribution make it perfect for commercial buildings
17. Older home renovations - Many older homes already use this system (often with diagonal planking under plywood)
18. Areas requiring maximum floor stiffness - The double layer cuts down floor deflection and movement
19. Luxury residential construction - This creates the perfect base for high-end flooring
Single-layer subfloors might work for basic jobs, but double layers excel in demanding situations. Yes, it is one of the best subfloor options available for maximum floor stability, even with newer alternatives on the market.
MgO Subfloor Panels
MgO subfloor panels are revolutionizing the building industry. These mineral-based panels give builders a solid alternative that combines fire resistance with structural strength.
MgO Subfloor Panels key features
MgO panels combine magnesium oxide with non-organic minerals and fiberglass mesh reinforcement. The panels stand out because of these characteristics:
·      The panels char instead of burning and stay structurally sound when exposed to flames
·      They handle moisture exceptionally well without breaking down
·      The panels weigh about 20% less than Portland cement boards
·      They stay stable with minimal expansion or contraction when moisture levels change
·      The non-toxic formula contains no harmful chemicals like silica, formaldehyde, or VOCs
A single 3/4" MgO panel can replace several layers of other materials. This saves money on materials and cuts down installation time.
MgO Subfloor Panels pros and cons
Pros:
·      Fire resistant without needing extra treatments
·      Better moisture resistance than wood-based products
·      Natural resistance to mold, mildew, and insects
·      Great thermal and acoustic insulation
·      Stays strong even after water exposure
·      Survives 25 cycles of water immersion with minimal strength loss
Cons:
·      Costs more than traditional wood-based subfloor options
·      You need special cutting tools with diamond-tipped blades
·      Some regions have limited availability which can delay projects
·      More brittle compared to wood products
·      Doesn't hold nails as well as wood-fiber materials
·      Surface finishing needs extra steps
MgO Subfloor Panels pricing
Here's what you can expect to pay for MgO subflooring:
Type | Thickness | Approximate Cost |
Standard MgO Subfloor | 3/4" (18-20mm) | $145 per 4'×8' sheet |
Fire-Rated MgO Panel | 3/4" (18-19mm) | Variable pricing based on fire rating |
The original cost might be higher than traditional options. However, homeowners often save money in the long run through better durability and less maintenance.
MgO Subfloor Panels best use cases
These panels work best in specific situations:
20. Fire-rated floor assemblies – A vital component for commercial and multifamily buildings that need extra fire protection
21. Moisture-prone environments – Perfect for basements, bathrooms, and kitchens where moisture resistance matters
22. Areas requiring superior sound insulation – Dense materials help reduce noise between floors
23. Health-conscious spaces – Non-toxic properties make these panels great for clean air environments
24. Commercial high-traffic areas – Their strength and durability suit heavy-use spaces
MgO subfloor panels deliver excellent performance where fire safety, moisture resistance, and structural integrity matter most. They create a reliable foundation that works well with almost any flooring material.
Delta-FL with Plywood Layer
Delta-FL with plywood layer offers a specialized subfloor system that solves moisture problems in concrete floors. This clever combination protects your finished flooring and makes it more comfortable to walk on.
Delta-FL with Plywood Layer key features
A dimpled, heavy-duty gray plastic membrane made from high-density polyethylene (HDPE) forms the system's foundation. The dimpled membrane creates a 5/16-inch air gap above the concrete slab. This gap lets water vapor pressure balance out and stops moisture from getting into your flooring materials.
This system does more than your standard moisture barriers:
·      Works as both a capillary break and vapor barrier
·      Makes floors feel warmer by creating a thermal break
·      Takes up minimal headroom - just 5/16-inch
·      This is a big deal as it means that the compressive strength is over 5,200 psf
Plywood or OSB sheets (usually 7/16-inch minimum thickness) go on top of the membrane to complete the system. You get a stable, dry base that works with almost any flooring material. Some types of flooring, like laminate, can go right on top of Delta-FL without the wood layer.
Delta-FL with Plywood Layer pros and cons
Pros:
·      Blocks moisture while letting concrete breathe
·      Creates warmer floors thanks to the thermal break
·      Health-conscious homeowners love the non-allergenic materials
·      Quick and simple installation
·      Comes with a 20-year product warranty
Cons:
·      Most flooring types need extra materials (plywood/OSB)
·      You must tape seams with special moisture-proof tape
·      Installation takes more steps than simple subfloors
·      Total height increases by about 3/4-inch with plywood
·      Costs more upfront than budget-friendly moisture barriers
Delta-FL with Plywood Layer pricing
Here's what you can expect to pay:
Component | Cost (USD) |
Delta-FL membrane | $1.30 per square foot |
OSB/Plywood layer | Varies by thickness |
Combined system | Starting at $0.43 per square foot |
The combined cost might seem higher than simple subfloor options at first. Notwithstanding that, homeowners find value in the moisture protection and comfort benefits, especially when you have basement installations.
Delta-FL with Plywood Layer best use cases
The system really stands out in these specific situations:
25. Basement renovations - Perfect for below-grade concrete floors where moisture never seems to go away
26. Directly beneath laminate flooring - You can install laminate "click-lock" systems right over Delta-FL with just the recommended foam underlay
27. Under carpet, vinyl, or hardwood - Add the plywood/OSB layer and you can use almost any flooring material
28. Cold concrete floors - Your floors will feel more comfortable and reach room temperature faster thanks to the thermal break
Basements benefit the most from this system. Traditional subfloor materials often don't deal very well with moisture exposure, but Delta-FL tackles both moisture vapor issues and cold floor problems at once.
Single Layer OSB Subfloor
Single layer OSB subfloor stands as the standard choice for budget-friendly construction projects. Oriented strand board (OSB) serves as North America's most accessible subflooring material, striking a practical balance between performance and cost.
Single Layer OSB Subfloor key features
OSB panels combine 3-inch to 4-inch wood strands in crossing patterns that are bonded with adhesives and pressed into sheets. This process results in panels without laps, gaps, or voids. Tongue-and-groove (T&G) designs are common in OSB panels, which come in standard 4' x 8' dimensions. The 23/32" thickness works best with joists placed 16 inches apart.
OSB delivers consistent strength across the entire panel, unlike plywood with its knots and imperfections. The manufacturing process compacts about 50 layers of strands into one sheet, creating a denser final product.
Single Layer OSB Subfloor pros and cons
Pros:
·      Costs 10-20% less than plywood
·      More structurally consistent than plywood
·      Available in larger panel sizes
·      Made from fast-growing, green trees
·      Twice the horizontal shear strength of plywood
Cons:
·      Absorbs water more slowly but retains moisture longer than plywood
·      Prone to irreversible edge swelling when exposed to water
·      Heavier and more brittle than plywood
·      Less nail-holding power than plywood
·      Not recommended under ceramic or vinyl tiles
Single Layer OSB Subfloor pricing
OSB subfloor panels range from $2.20-$4.50 per square foot installed, making them one of the most budget-friendly subflooring options. A standard 4' x 8' sheet of 23/32" OSB costs around $16.00, compared to plywood's $21.00 per sheet.
Single Layer OSB Subfloor best use cases
OSB subflooring works best beneath carpet and pad installations. The material shows excellent performance under engineered wood flooring and laminate. LP Top-Notch and similar water-resistant OSB products offer improved performance in basements or areas with moisture exposure.
The material's superior horizontal shear strength makes it ideal for attics and sheds. Bathrooms and water-prone areas should avoid OSB unless proper moisture protection is applied.
Comparison Table
Subfloor Option | Material Composition | Moisture Resistance | Installation Complexity | Approximate Cost (2025) | Best Use Cases | Main Advantages | Main Disadvantages |
AdvanTech Subfloor Panels | Engineered wood with advanced liquid resin technology | Superior | Moderate (requires adhesive) | $33.60 per 4'x8' sheet | High-end residential, moisture-prone areas, under premium flooring | Superior moisture resistance, exceptional strength, lifetime warranty | Higher original cost, not approved for exterior use |
DRIcore Subfloor Tiles | OSB with polyethylene moisture barrier base | High | Easy (DIY-friendly) | $6.00-$9.00 per 2'x2' panel | Basements, DIY renovations, cold concrete floors | Easy installation, creates thermal break, moisture protection | Expensive compared to traditional options, limited insulation (R-1.4) |
PVC and WPC Boards | 70% virgin polymer, 15% additive, 15% wood powder | Exceptional | Moderate | $8-30 per m² | Moisture-prone areas, spaces with termite problems | Waterproof, termite-proof, low maintenance | Temperature sensitive, higher original cost |
Double Layer Plywood Subfloor | Two layers of plywood/OSB | Moderate | Complex | $4.11-$6.28 per sq ft | High-traffic areas, beneath brittle flooring | Superior strength, reduced squeaks | Higher material costs, increased installation time |
MgO Subfloor Panels | Magnesium oxide with fiberglass mesh | High | Complex (requires special tools) | $145 per 4'x8' sheet | Fire-rated assemblies, moisture-prone areas | Fire resistant, mold resistant | Higher cost, brittle nature |
Delta-FL with Plywood Layer | HDPE membrane with plywood/OSB top layer | Excellent | Moderate | $1.30 per sq ft (membrane only) | Basement renovations, cold concrete floors | Effective moisture control, thermal break | Requires additional materials, complex seam taping |
Single Layer OSB Subfloor | Oriented strand board | Moderate to Low | Easy | $2.20-$4.50 per sq ft installed | Simple residential construction, under carpet | Economical, structurally consistent | Poor moisture resistance, less nail-holding power |
Conclusion
Your project's longevity, comfort, and success depend by a lot on picking the right subfloor. This piece explores seven budget-friendly subfloor options that work well for different needs without breaking the bank. Without doubt, each material has its own advantages based on what you need.
AdvanTech panels work great in high-moisture environments, and DRIcore tiles give you a simple DIY solution for basements. On top of that, PVC and WPC boards are exceptional at handling water in bathrooms and kitchens. The tried-and-true double-layer plywood system still gives unmatched stability for premium flooring. MgO panels are your best bet for fire resistance among other moisture-protection features.
A tight budget doesn't mean you have to settle for less quality. Delta-FL with plywood creates a moisture management system that works well and won't cost you too much. Simple residential projects with minimal moisture issues can use single-layer OSB, which remains the most economical choice.
Let your project's specific needs guide what you pick. Look at moisture exposure, floor traffic, how complex it is to install, and what kind of finished flooring you want. Cheaper options might look good at first, but spending a bit more now could save you big money on repairs down the road.
After testing these materials over the last several years, I've learned one thing – the best subfloor isn't always the priciest one. It's the one that fits your needs perfectly. This piece gives you the knowledge to protect your home and flooring investment for years, no matter what your budget looks like.